Robotics automation can be easier to build than you think. Here's an example of how a 5-axis SCARA robot can be built in-house with off-the-shelf products.
Overview
This is an in-house SCARA robot (AKA horizontal articulated robot) that automates work pick-and-place and transport between processes. It is used in automated production lines for gluing, measuring, and assembly, which were conventionally done manually. We built a SCARA robot in-house because we needed to a pick-and-place to transport small parts between processes in a limited space. Traditional robots typically are large and cannot be customized to fit in tight spaces.
Number of axes | 5 axes (3 links + lift + electric gripper) | |
---|---|---|
Robot control | Robot controller MRC01 | |
Payload | 0.7 kg | |
Maximum speed | 500 mm/s (maximum speed at gripper tip) |
|
Maximum speed of each axis | Axis 1 | 500 mm/s |
Axis 2 | 500 mm/s | |
Axis 3 | 500 mm/s | |
Axis 4 | 40 mm/s | |
Axis 5 | 156 mm/s (both sides) | |
Device main power | 115 VAC | |
Drive/control power supply | 24 VDC | |
Mass (SCARA robot part) | 4 kg |
System Configuration
The SCARA robot is controlled by Ethernet/IP from a host controller, such as a programmable logic controller (PLC). The MRC01 robot controller communicates to all AZ Series drivers via RS-485 communication (Modbus RTU).
Component List
Product name | |||
---|---|---|---|
Axis 1
|
![]() ![]() |
Hollow rotary actuator | DGM85R-AZAK |
Driver (Built-in positioning function type) | AZD-KD | ||
Flexible connection cable | CC030VZR2 | ||
DC power cable | CC02D010-3 | ||
Cable for RS-485 communication | CC001-RS4 | ||
Axis 2
|
![]() ![]() |
Hollow rotary actuator | DGM60-AZAK |
Driver (Built-in positioning function type) | AZD-KD | ||
Flexible connection cable | CC030VZ2R2 | ||
DC power cable | CC02D010-3 | ||
Cable for RS-485 communication | CC001-RS4 | ||
Axis 3
|
![]() ![]() |
αSTEP harmonic geared type | AZM24AK-HS50 |
Driver (Built-in positioning function type) | AZD-KD | ||
Flexible connection cable | CC030VZ2R2 | ||
DC power cable | CC02D010-3 | ||
Cable for RS-485 communication | CC001-RS4 | ||
Axis 4
|
![]() ![]() |
Compact cylinder | DR28T1A03-AZAKD-F |
Driver (Built-in positioning function type) | AZD-KD | ||
Flexible connection cable | CC030VZ2R2 | ||
DC power cable | CC02D010-3 | ||
Cable for RS-485 communication | CC001-RS4 | ||
Axis 5
|
![]() ![]() |
Compact gripper | EH3-AZAKH |
Driver (Built-in positioning function type) | AZD-KD | ||
Flexible connection cable | CC030VZ2R2 | ||
DC power cable | CC02D010-3 | ||
Controller
|
![]() |
Robot controller | MRC01 |
DC power cable | CC02D010-3 | ||
Cable for RS-485 communication | CC001-RS4 | ||
● EtherNet/IP TM is a trademark of ODVA. ● All motor cables are 3m long. ● All DC power cables are 1m long. ● The length of all cables for RS-485 communication is 0.1m. |
Total Estimated Cost | ~$11,969* |
*Typical 5-axis SCARA robots that meet the above requirements can cost between $15,000 to $25,000. This would be the lower end of the range, and it doesn't include any special features like vision systems. With this cost range, we can save between $3,031 and $13,031.
Introducing: MRC01 Robot Controller and MRC Studio Programming Software |
No ladder logic knowledge required.
Linkage between MRC01 and host system is directly controlled by EtherNet/IP. In-house robots can be easily added without making major changes to the control system of existing equipment.
The MRC01 can be easily set from initial settings to operation programs without specialized knowledge of programming languages. Initial settings such as selection of robot type and input of mechanism information are easy with a wizard. Targeted commands can be added to the operation program while moving the in-house robot with teaching operations. When one of our young equipment designers actually used it for the first time, he was able to create a program by teaching in about two hours because it was possible to set multiple axes with a single command.
It is possible to check the operation program of the in-house robot on the 3D simulator without driving the motor.
It supports vertical articulated robots, SCARA robots, and orthogonal robots, which are typical structures of industrial robots. The end effector axis can also be controlled by the MRC01, contributing to space-saving, wiring-saving, and cost reduction for the entire system.
Compatible with AZ series and electric actuators equipped with them. With a rich product lineup, we contribute to robot design with a high degree of freedom according to the robot type you want to manufacture in-house.
|
All of the motors, actuators, and drivers controlled by the MRC01 robot controller on the SCARA robot are from the αSTEP AZ Series family.
Products Used for Each Axis
Achieving sensor reduction and battery-less with a mechanical multi-rotation absolute sensor
All motors, actuators, and drivers used on the SCARA robot are from the same αSTEP AZ Series product family, so precision is guaranteed. With the same battery-free absolute encoder technology, external sensors on all axes can be eliminated, contributing to reduced wiring and a compact configuration. Absolute position information is retained even if the power supply is shut off due to an emergency stop or power failure during positioning operation. There is no need to worry about battery costs, operational troubles, or maintenance. In addition, the status of each axis can be monitored by the drivers.
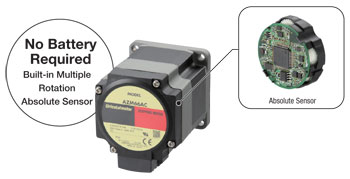
● DGⅡ Series Hollow Rotary Actuator (Axis 1, Axis 2)
Suitable for joint shaft Hollow rotary actuator and small geared type
When the SCARA robot grabs a workpiece at the tip of the arm away from axis 1, a large load moment is generated.
The DGII series uses cross-roller bearings for the hollow output table bearings to achieve a high allowable moment. This contributes to expanding the range of motion of the arm. In addition, hollow holes (through holes) can be used for wiring complicated cables, simplifying robot design.
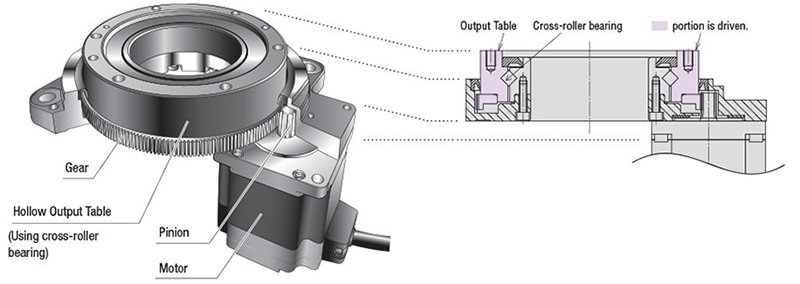
![]() |
![]() |
● αSTEP AZ Series Harmonic Geared Type (Axis 3)
Geared stepper motor with no backlash
Even a small deviation can become large at the tip of the arm, and it may not be possible to grip the workpiece accurately. The harmonic geared type has no backlash, so it suppresses misalignment and achieves accurate operation.
● DR Series Compact Cylinder (Axis 4)
Compact and lightweight actuator that reduces the load on the tip of the robot mechanism
The compact body that integrates the αSTEP AZ series and a ball screw contributes to the miniaturization and space-saving of equipment. By reducing the weight of the tip of the device, you can expect to improve the degree of freedom in design.
● EH Series Compact Gripper (Axis 5)
Grip small parts delicately
As the end effector becomes smaller and lighter, the burden on each joint can be reduced, contributing to the size reduction and cost reduction of the entire robot. The position, gripping time, and gripping force can be freely set with the electric gripper. Various grips can be achieved.
We support robot design from the product selection stage
Motor sizing and selection
Our dedicated staff will size and select the motor for you. Please download the selection request form, fill in the necessary items, and send it to us. We can even use materials you have on hand, such as schematic diagrams, image diagrams, and CAD data of the mechanism.
* User registration and login are required.
Additional support/materials available
We are working to update our website to include additional support for other types of robots and materials for robotics integration. Please ask our team for the most updated information for your specific robot.
We're here if you need help
If help is needed, our technical support engineers and application engineers can respond to various questions regarding motor sizing, motor selection, setup, wiring, and programming.