An end effector, such as an electric gripper, is an essential part of industrial robots. More importantly, using the right gripper for the load being transferred prevents damage while improving automation efficiency. In this article, we share how one system integrator has successfully adopted an electric gripper for one of their articulated robots.
Tokuden Co., Ltd. is a factory automation (FA)/robot system integrator mainly in the Shizuoka Prefecture in Japan. They provide manufacturing and robotic solutions to a wide variety of customers in the automobile, textile, pharmaceutical, and food industries. In addition to sharing feedback on our compact electric gripper, they also shared how they approach robotics as a system integrator.
Topics covered:
- Using compact electric grippers to precisely control gripping force and reduce weight.
- The number of requests for industrial robots is increasing.
- Use a lab/showroom for proof-of-concepts.
- Wiring, compatibility, and connectivity with peripheral devices are also important factors in end effector selection.
- Compact size and reasonable pricing make EH Series grippers effective in a proposal.
Using compact electric grippers to precisely control gripping force and reduce weight
A customer of Tokuden had trouble coming up with the right automatic production equipment for picking up and transferring delicate workpieces gently. They considered using a pneumatic gripper. However, the inconsistent gripping force provided by the pneumatic gripper can damage the workpiece, and reducing the air pressure could cause the workpiece to drop.
By using an electric gripper, the gripping force can be stable and can be effective when handling delicate workpieces. In addition, electric grippers do not need additional air tanks and hoses to provide pressurized air, so installation restrictions and required maintenance can be eliminated.
The adopted EH Series compact electric gripper offers precise control of gripping force and is compact and lightweight. It is not affected by installation location restrictions within the equipment, and productivity was increased by using two axes of gripping mechanisms within the same equipment, and the equipment is still operating stably."
The director of Tokuden Fuji Sales Office, Mr. Ota, who is actually in charge of customers, said the following about the EH Series, "We have been able to kill two birds with one stone and have received high praise from our customers."
"We have been able to kill two birds with one stone and have received high praise from our customers."
When asked about the demand and differences between pneumatic grippers vs electric grippers, Mr. Ota pointed out that they use about a ratio of 50:50 between pneumatic grippers and electric grippers. Pneumatic grippers are cheaper and are used to grip workpieces that aren't delicate. Electric grippers are used when the gripping force must be adjusted or controlled precisely. With delicate workpieces, even a small scratch could mean a scrapped workpiece.
Mr. Ota said, "The key point with electric grippers is that the gripping force can be adjusted electrically. With precision products, if the workpiece gets scratched, you will receive a complaint. We check the shape and machining precision of the customer's workpiece before proposing an appropriate gripper."
The number of requests for industrial robots is increasing.
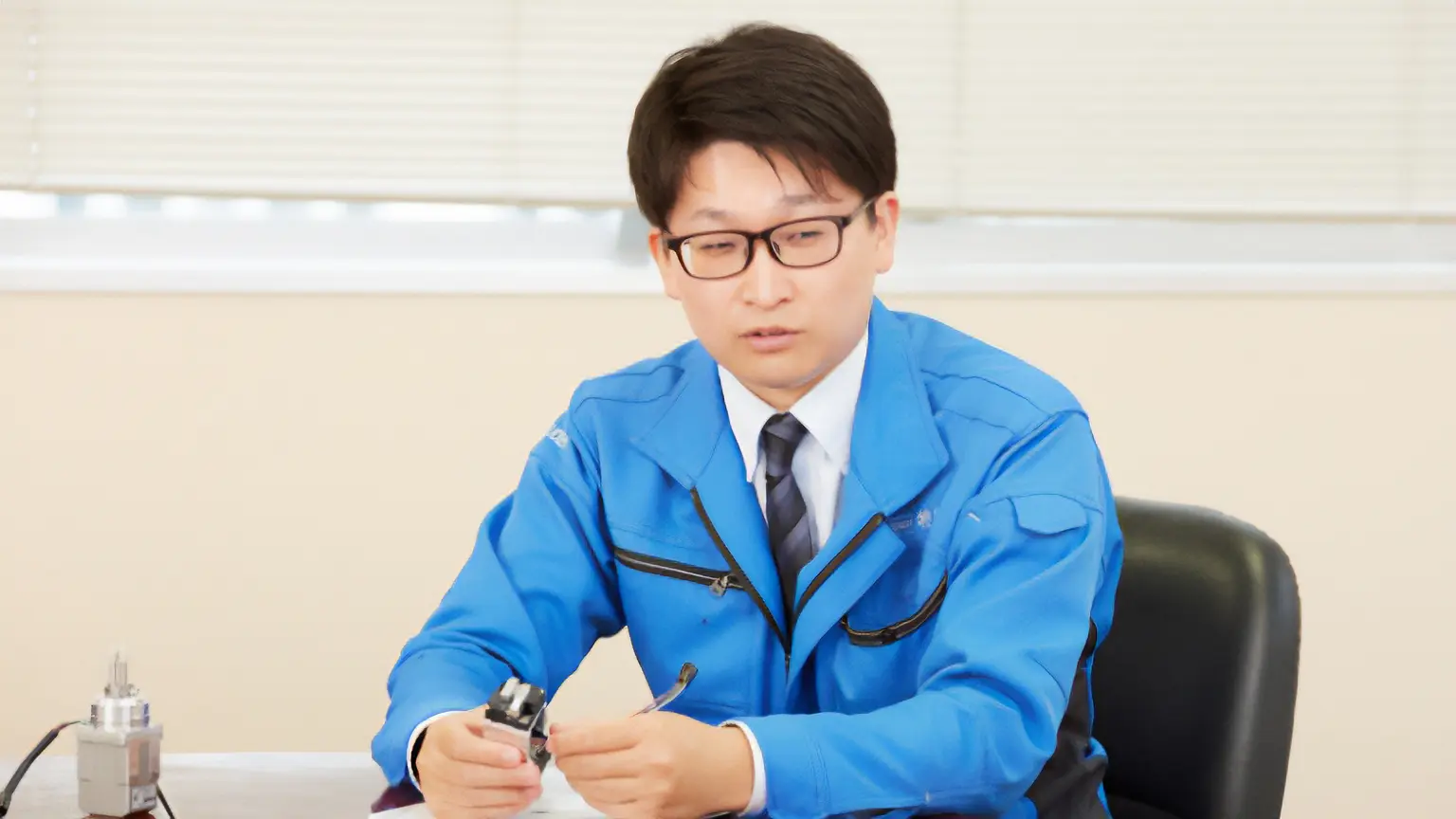
When asked about the type of inquiries received, Mr. Kameyama, Section Manager of Sales Technology Division, revealed that inquiries regarding robots are increasing overall. Recently, they have received requests to build the entire system, but the requests also include training for operators who will handle the robot's operation and maintenance.
When asked about the changes in customer demand or usage of industrial robots, Mr. Suzuki, Sales Engineering Department Group Leader, explained that it depends on the size of the company. Large enterprise customers seem to be adopting robots at an accelerated pace. In multi-product production sites, equipment modifications (setup changes) are required for each product. By introducing robots, costs are reduced by simply changing the programming and eliminating the need to modify or replace the equipment. Additionally, some customers are using more robots to improve branding. On the other hand, when it comes to small and medium-sized enterprises, robot adoption is not as much as large enterprises. Often, robot implementations are introduced by a third-party company like system integrators.
For small and medium-sized business customers, Mr. Suzuki says, "The timing often coincides with the launch of a new line. Orthogonal axes typically only do one task, so in the right scenarios, we propose articulated robots that can do a variety of tasks."
Mr. Kameyama says, "Recently, customers are often performing a lot of research themselves, and we are increasingly being asked if something is possible with robotics. I believe that we must pay attention to the latest technological trends in order to make the best proposals to our customers."
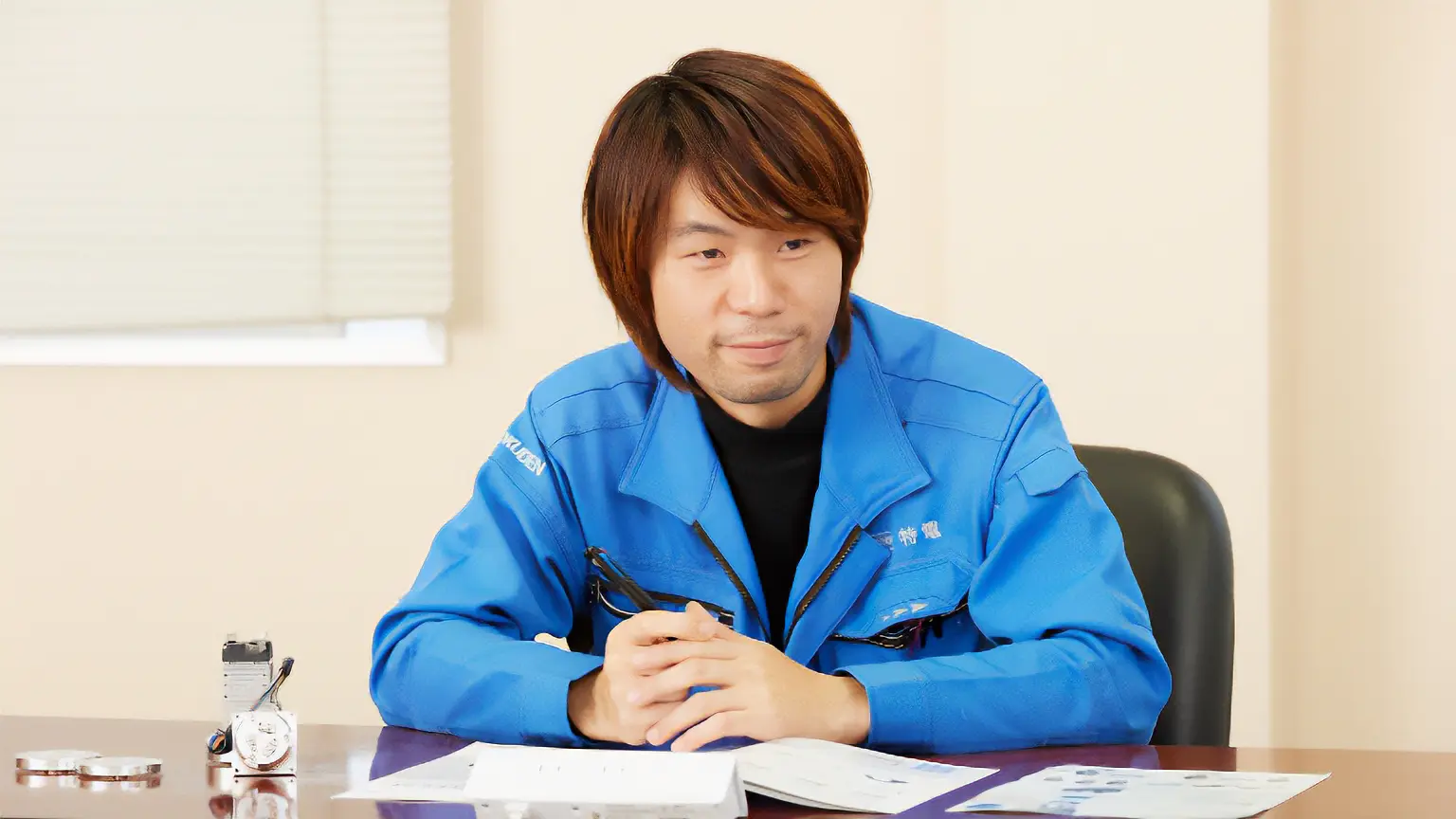
Use a lab/showroom for proof-of-concepts.
When asked about how they introduce robots, Mr. Suzuki explained that there are two main methods. There are cases where the entire system is built and cases where they sell the robot individually. When it comes to system construction, they listen to the customer's requests and develop a concept from scratch.
Mr. Kameyama pointed out that customers who purchase robots individually have different purposes, depending on whether they are a large company or a small company. In the case of large corporate customers, there are many cases where they are challenged with coming up with creative ways of using the product. For example, a collaborative robot might be used in conjunction with a transportation robot like an AGV or an AMR to automate more of the process. Small and medium-sized enterprises often purchase our products in order to strengthen their own technical capabilities and since they are not robot experts themselves, after-sales support is expected. The smaller customers set up the system, but they still need advice on how to use the robot.
As part of their robot introduction efforts, Tokuden opened a Robot Lab in June 2020. Many of their customers are not very familiar with robots and have never touched the controls of an actual machine. Their Robot Lab provides a site where different types of grippers can be used and tested; such as pneumatic grippers, electric grippers, and suction grippers. When a customer visits, a general introduction is given for different types of robots and end effectors, so the customer can get an idea of what's possible with current technologies and different vendors. After a general understanding is established, then the customer explains what they need to do, and Tokuden works with different teams to make it happen from concept to implementation.
Ms. Kurihara from the Sales Planning Division said, "Many customers are not very familiar with robots and have never touched an actual machine. When customers visit, I explain everything on my side, and after that, I ask them what they are interested in and what they want to do with the robot, and we work together to come up with a solution."
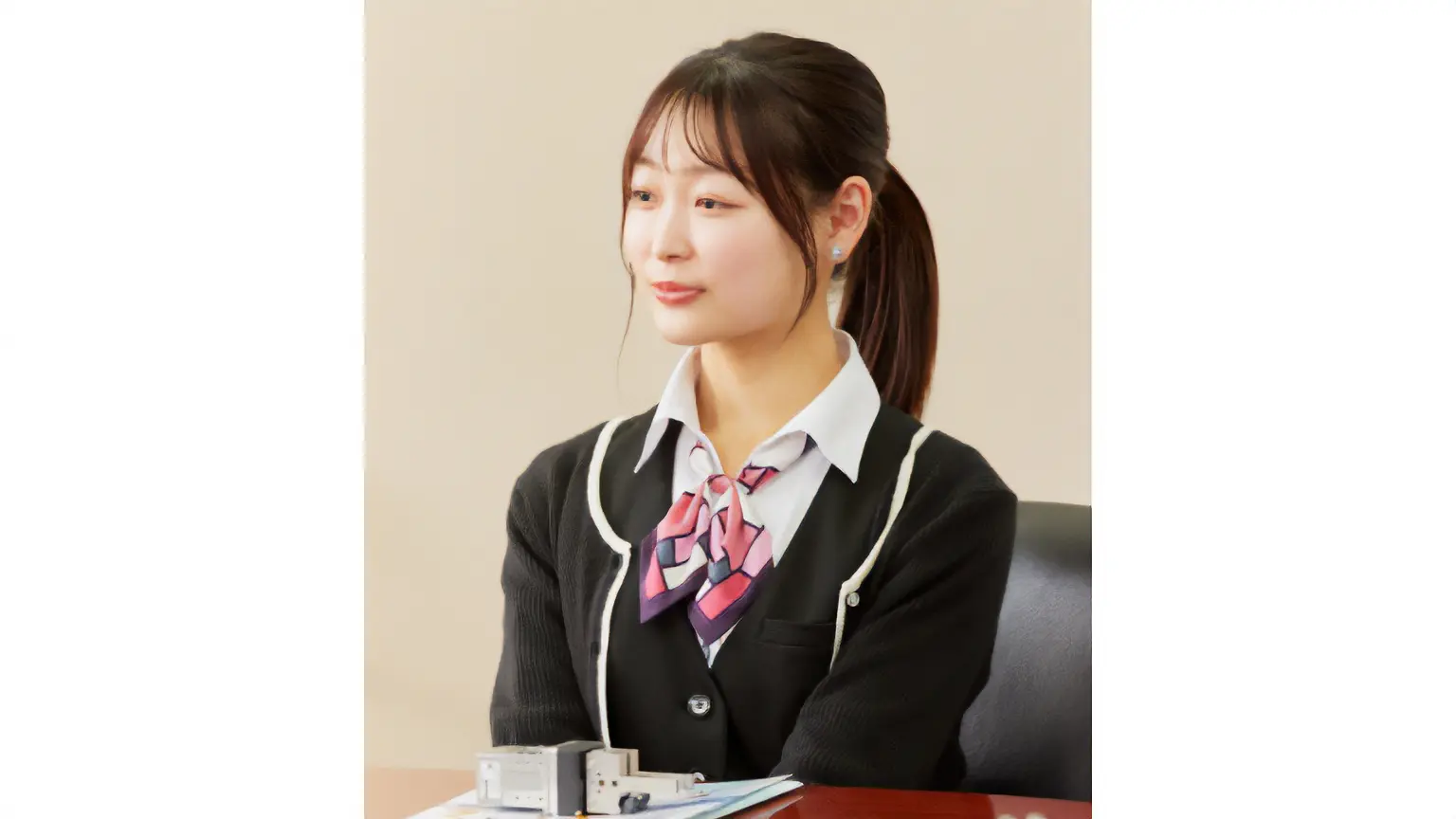
Wiring, compatibility, and connectivity with peripheral devices are also important factors in end effector selection.
When proposing robots to customers, in addition to fulfilling the application requirements, Tokuden also considers the maintenance aspect for their customers. If their customer already has a robot in place, they will suggest the same manufacturer as that robot manufacturer.
Since robots often work with other equipment, they also consider the robot's compatibility and connectivity with peripheral equipment. Using products from the same manufacturer is often easier and faster than using products from various manufacturers.
When it comes to selecting an end-effector, Tokuden looks for something that's appropriate for the work. In cases where customers can't use hydraulics or pneumatics, such as transferring delicate parts or where there's limited space available, an electric gripper is adopted for its precision and size.
Often overlooked is the wiring aspect, especially for articulated robot arms. If cables run along the outside of the arms, they will restrict their movement, so it would be easier if the cables could pass through the center of an arm, such as through a rotary actuator with a large hollow bore at its base. In the case of collaborative robots, there are grippers that can be mounted simply by connecting them to a connector.
Mr. Kameyama suggests that it's also important to choose a gripper with the right opening width. If the opening width is too small, the workpiece cannot be gripped. If the opening width is too large, it means it's oversized. In addition to the stroke length of grippers, Mr. Suzuki also thinks the way it opens is important. Even with parallel chucks, the gripping method and axis movement differ depending on the manufacturer, so these are also important points to consider when making a selection.
In terms of maintenance, electric grippers have the impression that they require a lot of effort to set up. Mr. Kameyama doesn't think so and actually thinks there are more problems with pneumatic grippers, where air blockages can cause temporary production stoppages. There are pros and cons to each type of gripper.
Regarding size, Mr. Suzuki will choose a compact gripper if there are space constraints. Availability and lead times are not a concern when introducing new robots. This is because robots take several months to be delivered, so there is no need for immediate delivery. Their customers are more concerned about whether or not they can get a replacement immediately if something breaks.
When asked what type of gripper needs to be developed, Mr. Suzuki says, "I want an electric gripper that is waterproof, dustproof, and highly durable. For example, the gripper may be taking out a drug from a freezer case or working in an environment where corrosive gases are generated. These grippers may be for special purposes, but I think that if the electric gripper can be used for such applications, the range of applications will increase."
Compact size and reasonable pricing make EH Series grippers effective in a proposal.
Oriental Motor has released the EH Series compact electric grippers equipped with an αSTEP AZ Series hybrid step-servo motor. A multi-turn mechanical absolute encoder is built into the rear of the motor for battery-less absolute position control, and the motor operates a rack and pinion mechanism to drive the base jaws back and forth. A two-finger type is shown below.
![]() |
![]() |
The EH Series offers a two-finger type gripper and a three-finger type gripper, and their small size and lighter overall weight reduce the burden on articulated robots as well as cartesian robots, which means smaller motors can be used on the other axes. The gripping force can be adjusted to a percentage of the operating torque, allowing delicate gripping without damaging the workpieces.
ISO9409-1-compliant installation flanges are also offered as an accessory to easily attach the gripper to commercially available articulated robots. As with any AZ Series equipped actuator, multiple industrial communication protocols are offered by the dedicated programmable driver to communicate to its host controller; including EtherNet/IP, EtherCAT, and Profinet.
![]() |
![]() |
As shown in the videos below, while the two-finger type gripper is designed to grip rectangular objects, the unique three-finger type gripper is designed to grasp round or cylindrical objects such as plastic bottles.
|
|
When asked to give an impression of the EH Series, Mr. Suzuki said, "Among the electric grippers that I know of, it's quite small. I've never seen anything this size, especially a three-finger electric gripper. I think there is an advantage in size. Also, the rotating and grabbing motion is unique. I think it's a gripping method that other companies don't offer."
"I've never seen anything this size, especially a three-finger electric gripper."
In addition, the small and lightweight "mini" driver, which supports a wide range of motors and linear actuators equipped with the AZ Series motor, can be installed near the electric gripper housing, allowing for shorter cables. The video below shows an example of a 7-axis robot arm with the "mini" drivers mounted near the motors; therefore simplifying the wiring.
Mr. Suzuki also said, "By installing a driver behind the electric gripper, it's ideal for industrial robots with a light payload. If you use the EH series, you will need a bellows cable cover because the cable will run outside the motor. Depending on the usage scenario, the cable's range of motion may be limited, so you may need to consider the cable placement."
Mr. Kameyama says, "From a sales perspective, the reasonable price compared to overseas products is also attractive. I would like to see certification from each robot manufacturer and easy plug-and-play connectivity. Even if you consider the increased cost, I think we can offer a proposal that is well worth the price."
Interview cooperation:
Tokuden Co., Ltd.
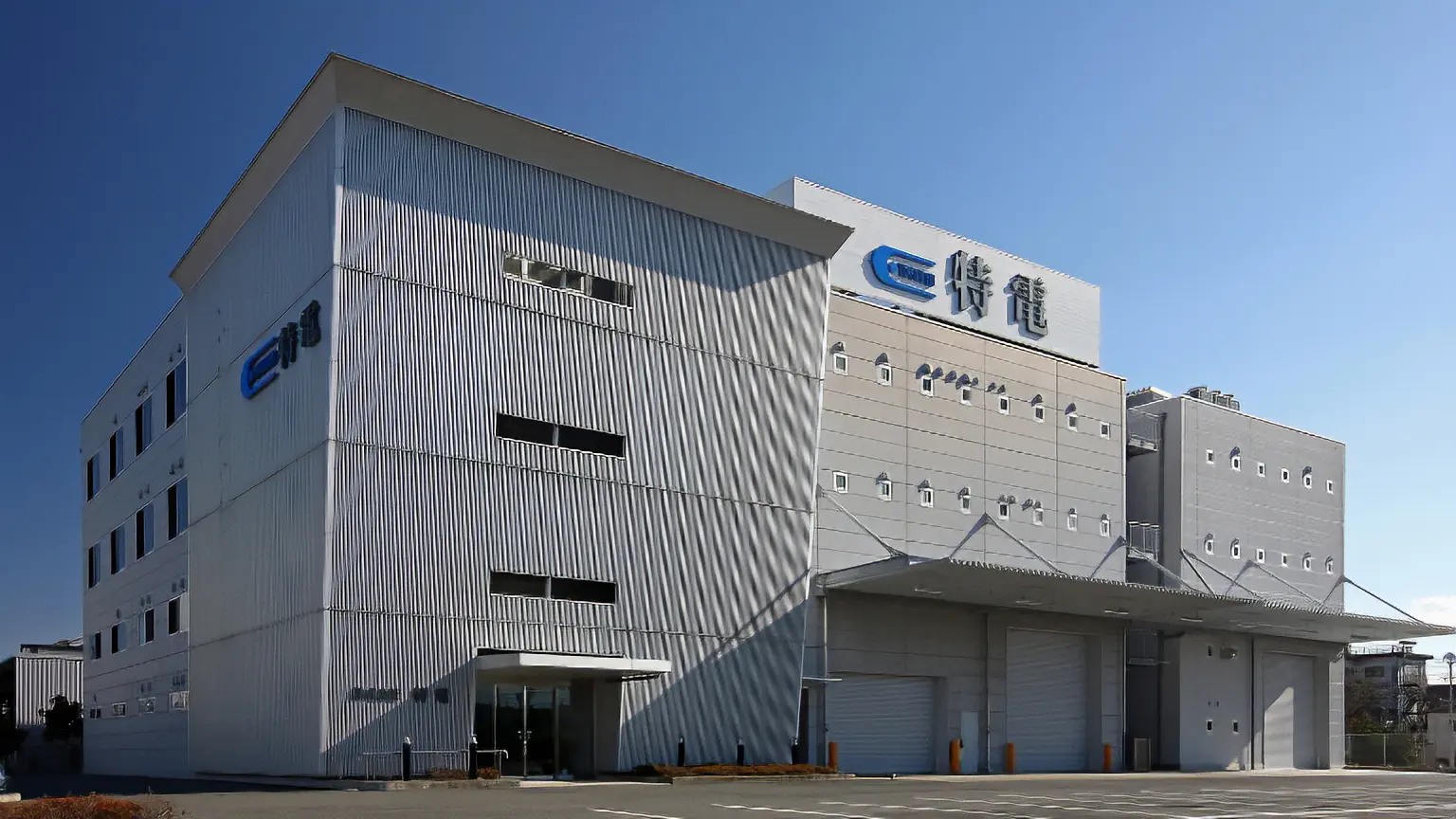
Interviewer: Oriental Motor Sales Division Product Planning Department Manager Yuki Arai