Parallel shaft AC gear motors are the standard configuration in the industry. However, right angle brushless gear motors are gaining popularity for their ability to minimize the footprint of a machine, such as a conveyor.
Another factor that should be considered is the type of gears used in the gearhead. While worm gear technology is popular, its gear efficiency can vary from 50~90% depending on gear ratio. On the other hand, hypoid gear technology keeps its efficiency at 80~95% regardless of gear ratio. Higher gear efficiency allows more torque to be transferred from the motor to the load shaft, and sometimes allows even smaller motors to be used.
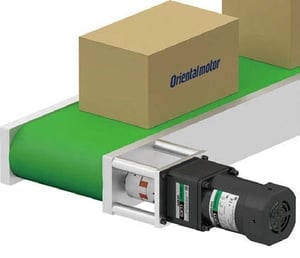
Conventional Equipment: An AC induction motor is installed on the conveyor with a parallel shaft gearhead and a coupling mechanism. An inverter (VFD) is typically used for speed control (not shown).
Problems with Conventional Equipment:
- The motor and transfer mechanism protruding on the side of the conveyor is taking up more space than it should. Therefore, it is difficult to add more conveyors side by side.
- The number of
parts and labor hours needed to install the motor on the equipment is excessive. - Parallel shaft gear motors typically use helical or spur gears, which feature less torque transfer efficiency than
hypoid gears.
SOLUTION: BMU Series brushless motor + JH gearhead + AC input driver
Use a compact and high power (right-angle hypoid type) to reduce the motor protrusion on the side conveyor. The efficient JH type gearhead also requires fewer parts to install to a conveyor (face mount or use a torque arm). Since both brushless motors and the JH gearheads are more efficient than AC motors and parallel shaft gearheads, the motor size and power consumption can also be reduced. To make it even easier to replace AC motors and inverters (VFDs), we
Advantages offered by BMU Series:
- JH right-angle hypoid gearhead features high rigidity, torque & efficiency
- Motor protrusion is reduced
- Motor size is also reduced
- Face mount (left) / torque arm (above)
- Fewer parts to install
RESULT: reduced labor hours by using fewer parts
how a right-angle gearhead can improve machine design & installation
Read the next post to see how much mass can be reduced by switching to brushless motors.