Gearheads play a crucial role in motor performance optimization. Each type of gear offers its own features and characteristics, and the gear ratio alters a motor's output torque and speed. By carefully selecting the optimal gear type and ratio, engineers can fine-tune motor performance to align precisely with the application requirements.
A motor becomes a gear motor when a gearhead is assembled with a motor. The gearhead case consists of a series of gears that can multiply a motor's torque but also reduce its speed by the same ratio. The gearhead also has an output shaft where the load attaches to.
Similar to a belt-and-pulley mechanism, where one pulley runs slower than the other due to the difference in the two pulley diameters, a gearhead's output shaft runs slower than the motor pinion shaft by the factor of its gear ratio. The advantage is that the gearhead is more rigid and can house a series of gears in a much smaller footprint than a belt-and-pulley mechanism.
In this article, I'll cover the types of gearheads offered for brushless gear motors and how to select one.
Topics covered:
- About Brushless Motors
- Gear Selection for Brushless Motors
- Motor Sizing Example - Belt Conveyor
- Summary
High Speed Stability
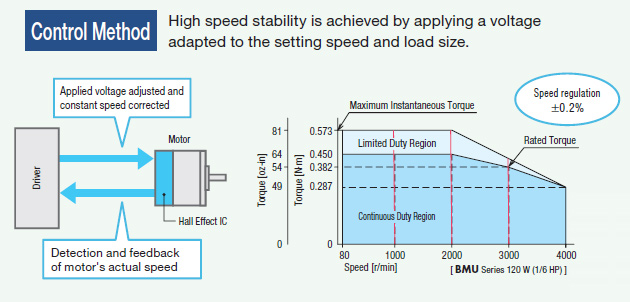
Space Saving
The compact yet powerful brushless DC motor incorporates permanent magnets in the rotor. Compared with an AC induction motor with a frame size of 3.54 in. (90 mm), a brushless DC motor of the same specifications is 62% shorter. With a much shorter length, a brushless motor is also 62% lighter than an AC induction motor of the same frame size.
The compact motor structure is helpful when downsizing equipment or reducing the load on an AGV/AMR.
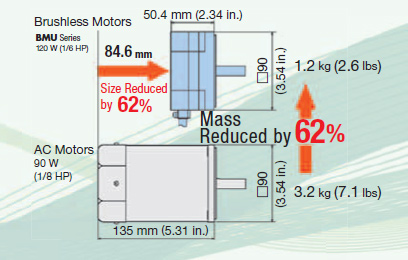
Energy Saving
Brushless DC (BLDC) motors, which incorporate permanent magnets in the rotor, generate little secondary loss from the rotor. Compared to AC induction motors, brushless motors can have up to 66% less loss. At an output power of 1/6 HP (90 W), for example, the power consumption of the BMU Series brushless DC motor is approximately 26% less than that of a VFD/inverter-controlled AC motor. In the same frame size, a brushless motor can output 1.3 times more power than an AC induction motor.
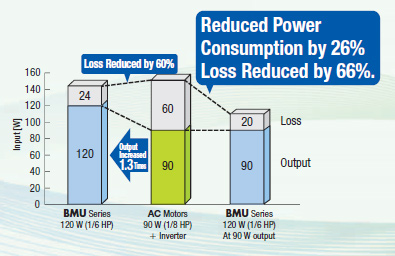
By attaching a gearhead to a motor, you can:
|
![]() |
For other advantages of geared motors, please read this article.
FYI |
When selecting gearheads, pay attention to the rotation direction of the gearhead shaft. Some gearheads reverse the shaft rotation with certain gear ratios.
|
Pararallel Shaft Gearhead (GFV gear type) | Up to 619 lb-in (70 Nm) | 10,000 hours rated life |
|
GFV gear type parallel shaft gearheads are compact and are the most common type of gearhead offered for brushless motors. They use a combination of helical and spur gears. These gearheads are offered for brushless motors ranging from 30 W to 400 W and can reach a permissible torque of 620 lb-in or 70 Nm. Gear ratios are offered from 5:1 to 200:1. They have a long life rating of 10,000 hours. High strength and low noise characteristics are achieved through improved case rigidity, carburized and hardened gears, and more precise assembly technology. The high permissible torque is 2 ~ 3 times that of a gearhead for an AC motor with the same frame size. With the gearhead's boss and machined mounting surface, the installation accuracy has also been greatly improved. This gearhead is rated for long life and uses a special bearing and grease for high speed rotation. A rated life of 10,000 hours is achieved. Both IP66 and IP67 versions are offered, and an H1 food-grade grease option is available.
Availability: all product series |
FR Hollow Shaft Flat Gearhead (GFS gear type) | Up to 940 lb-in (106 Nm) | 10,000 hours rated life |
![]() |
FR hollow shaft flat gearheads provide high permissible torque axially without saturation even at high gear ratios. The unique case design allows larger bearings and gears for higher strength. Like a right-angle gearhead, they can also help save space and eliminate components such as couplings. These gearheads are offered for brushless motors ranging from 30 W to 400 W and can reach a permissible torque of 940 lb-in or 107 Nm. Gear ratios are offered from 5:1 to 200:1. They have a long life rating of 10,000 hours.
Availability: all product series |
CS Centered Shaft Gearhead (Spur) | Up to 30 lb-in (3.38 Nm) | 10,000 hours rated life |
![]() |
Compared to the parallel shaft gearhead (GFV), the CS centered shaft spur gearhead offer higher permissible axial and radial load. It can achieve 1.6 times more torque with the same frame size. The centered output shaft helps simplify machine designs and installation. These gearheads are currently offered for stepper motors and smaller brushless motors ranging from 30 to 50 W and can reach a permissible torque of 30 lb-in or 3.39 Nm. Gear ratios are offered from 5:1 to 20:1 only. They have a long life rating of 10,000 hours.
Availability: BLH Series, PKP Series |
👍 For High Torque:
JV Gearhead (Flange Mount Type) | Up to 3,814 lb-in (431 Nm) | 5,000 hours rated life |
![]() |
JV type gearheads are rated for IP66 and offer superior mechanical strength. They can be directly installed by using the flange surface. These gearheads are offered for brushless motors ranging from 200 W to 400 W and can reach a permissible torque of 3814 lb-in or 431 Nm. 2 gear ratios are offered: 300:1 and 450:1. They have a long life rating of 5,000 hours.
Availability: BMU Series, BLE2 Series |
JB Gearhead (Foot Mount Type) | Up to 5,159 lb-in (583 Nm) | 5,000 hour rated life |
![]() |
JB type gearheads are rated for IP44 and offer high rigidity and permissible torque. Due to the built-in foot mounts, no external mounting bracket is necessary. These gearheads are offered for brushless motors ranging from 200 W to 400 W and can reach a permissible torque of 5159 lb-in or 583 Nm. Gear ratios are offered from 5:1 to 1200:1. They have a long life rating of 5,000 hours.
Availability: BMU Series, BLE2 Series |
JH Gearhead (Right-Angle Hypoid Type) | Up to 1,575 lb-in (178 Nm) | 5,000 hours rated life |
![]() |
JH type gearheads offer high permissible axial load, high permissible radial load, and stainless steel hollow shaft in a right-angle orientation. The hypoid gear it employs offers higher efficiency than other types of gears like worm gears. Like any right-angle gearhead, use it to save space or eliminate components like a coupling. These gearheads are offered for brushless motors ranging from 60 W to 400 W and can reach a permissible torque of 1575 lb-in or 178 Nm. Gear ratios are offered from 5:1 to 200:1. They have a long life rating of 5,000 hours.
Availability: BMU Series, BLE2 Series |
FYI |
Typically, the combined specifications for the gearmotor are already listed by the manufacturer, so all you have to do is verify the numbers. However, if you purchased a motor and a gearhead from different manufacturers, then you'll have to do some calculations to determine the final output. The torque at the gearhead output shaft is the motor torque multiplied by the gear ratio and gear efficiency:
Permissible Torque TG = TM × i × η
T.G. = Gearhead Permissible Torque T M = Motor torque i = Gearhead reduction ratio η = Gearhead transmission efficiency The gearhead output shaft speed is the motor output shaft speed divided by the gear ratio. |
Brushless Motor Sizing Example - Belt Conveyor Goal: Determine if the gearhead + motor will satisfy your torque, load inertia, and speed range requirements.
There are many formulas to calculate the required torque. The trick is knowing which one to apply.
Motor Sizing Example - Belt Conveyor
![]() For the belt conveyor example above, here's the formula to calculate the required "load torque".
![]() Calculate your required torque and add an adequate safety factor. Make sure this value is under the permissible torque specification of the motor + gearhead.
Next, add up all load inertia values of objects that are driven by the motor. In a conveyor, you would calculate for the pulleys and the load being moved linearly. Make sure the total inertia value value is within the permissible load inertia of the gearhead + motor. The formula used to calculate load inertia depends on the mechanical setup. Make sure to use the right formula to calculate your load inertia and provide adequate safety factor if necessary.
Inertia of a Cylinder or Disc (as from the X or Y-axis)
Example: Inertia of a Load in Linear Motion
Lastly, determine your required speed range and verify whether it is within the capabilities of the motor and gearhead.
Also, check if the gearhead can handle your axial and radial loads.
![]() Refer to the specifications of the gearhead or gearmotor for the axial load (AKA: thrust load) and radial load (AKA: overhung load) specifications. They should be in newtons or kilograms. Your axial load and radial load should be under the max values.
For more information about motor sizing calculations and formulas, please refer to our motor sizing notes series or a conveyor sizing and selection example.
With the required torque, load inertia, speed range, axial load, and radial load, you now have the right information to select an optimal gearhead and gear ratio. Other things to consider include how high of an IP rating you need, how the gearhead fits into your design (right-angle shaft vs parallel shaft), and, of course, how much you can afford. Sometimes, you can't have everything you want, so it's important to separate the must-haves from the nice-to-haves that might not be necessary for the application.
|
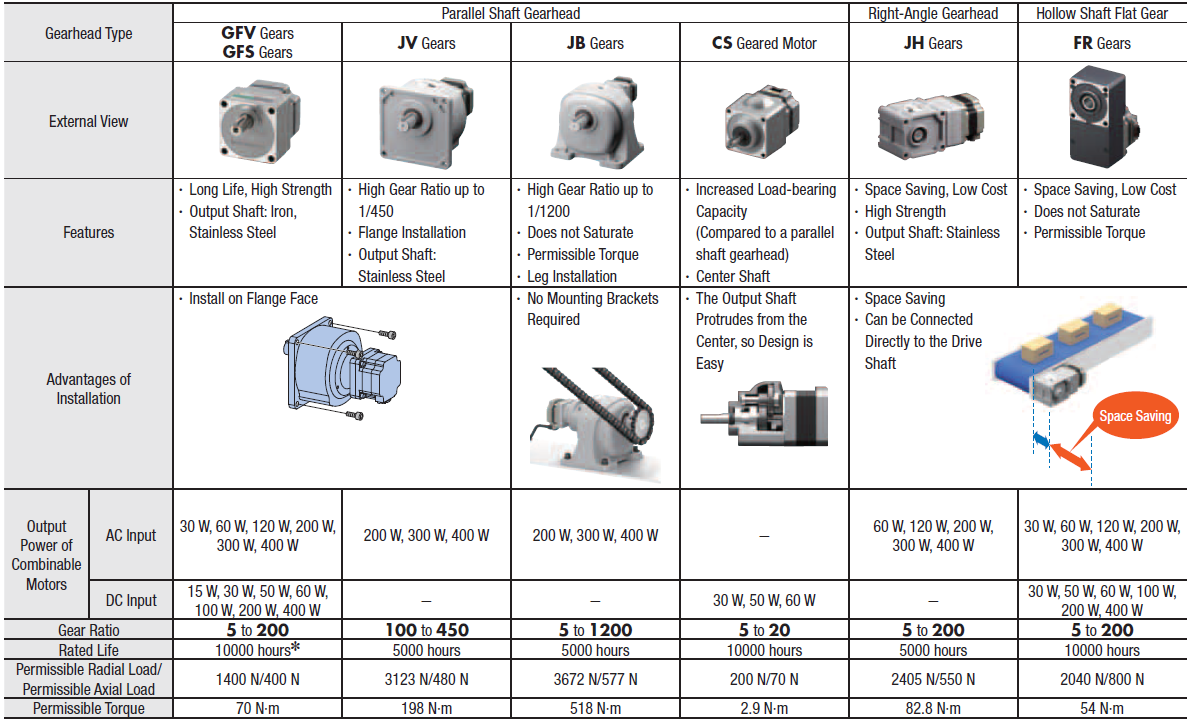
The values for permissible radial load, permissible axial load, and permissible torque are for the following operating conditions. They will vary based on the combined motor output power and gearhead gear ratio.
· Output Power : 200 W (For CS geared motors, values are for 50 W models.)
· Motor Shaft Speed: 3000 r/min
· Gear Ratio : Maximum gear ratio for each gearhead (Example: For GFV gear, the gear ratio is 200)